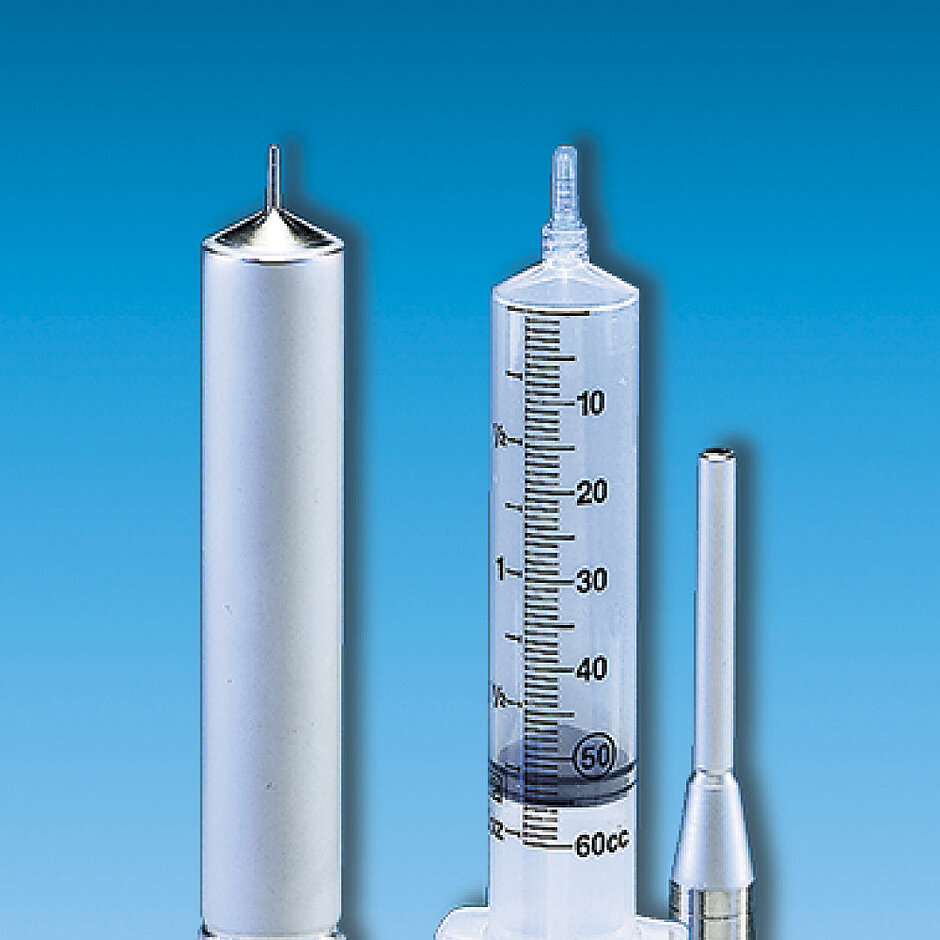
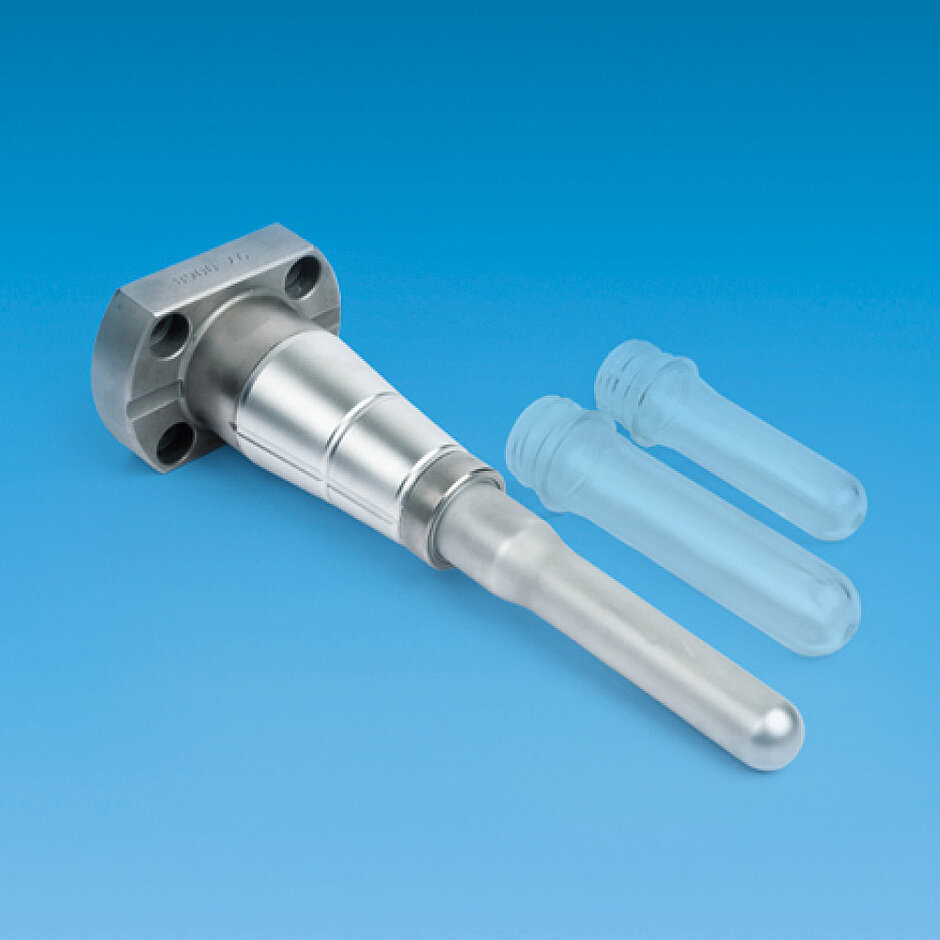
TOPOCROM® easyeject for dies
The use of TOPOCROM® coated dies for plastic injection molding has proven itself for many years. Compared to other types of coated or structured surface, TOPOCROM® achieves considerably better results in a variety of way.
Advantages on the molding tool
- Better ejection
- Up to 30% quicker cycle times
- Little or no release agent is required
- Less pressure and effort during demolding
- Better heat distribution over the complete mold surface
- High resistance to wear and corrosion
Advantages for the plastic part
- Better heat distribution on the plastic work-piece
- The option of smooth or structures surfaces
Cost-effective rework of used injection molding tools
If there is no mechanical damage to the base material, the tool can be recoated after de-chroming without any interim machining.
A wide choice of materials
As the maximum coating temperature in the TOPOCROM® reactor is <70° C, there is a wide range of mold materials to choose from.
During melting, the internal friction (dissipation) in the material is mainly used. The conveying principle overcomes the counterpressure of the extrusion die and forms the melt. The semi-finished product is then calibrated, cooled and brought to size.
The coating of the plastic and rubber injection moulds with TOPOCROM® easyeject enables major production advantages: Better demoldability, faster cycle times, less release agent, less wear.
The special surface structure and the ability to transport lubricants or release agents are the reasons for the excellent properties.
The TOPOCROM® easyeject coating contributes to cost optimisation through reduced use of raw materials and energy. It enables more frequent product changes with decreasing batch sizes. Less waste is produced during material change processes. Last but not least, the processes during product change are optimised.
Studies at the Institute for Production Engineering IPE at the university of Duisburg prove that TOPOCROM® coated extrusion tools show measureable advantages compared to other surfaces. They analysed the product changing behaviour during single screw extrusion and diagnosed amongst others a significant influence of tribology on this process.
The characteristics of the structured layer (roughness, wettability, open or closed structure, Rz-values) can be defined precisely during the coating process. The use of TOPOCROM® coated tools shows the following advantages:
- Avoiding deposits
- Significantly less abrasion
- Better flowing ability
- Longer service life