Structured surfaces for any demand
TOPOCROM® is a technology for producing structured TOPOCROM®-layers in a continuous single process step (reactor coating). Individually adjustable surface topographies are available according to the demands of the customers.
Schematic illustration of a TOPOCROM®-coating. The distinctive hemispherical surface structure shows resp. enables different characteristics in industrial processes.
Surface topography and multi-layer system
Depending on the demands and the base material the multi-layer system is chosen. The surface topography is selected individually and specifically according to the intended application (e.g. abrasion-resistance, embossing property of skin-pass rolls, grip effects of feeder rolls). It is possible to generate open or closed structures, high or low roughness values.
To achieve the desired features of the surface we proceed as follows:
- Formulation of the desired technical properties (specification sheet)
- Coating of a work-piece for real use (sampling)
- Optimizing the coating parameters if necessary (fine-tuning of the coating process)
- Coating of serial resp. single parts under constant quality control
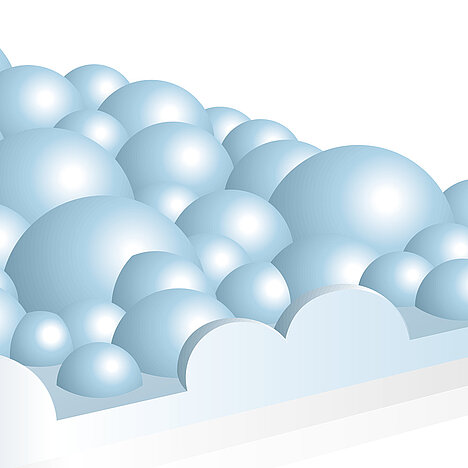
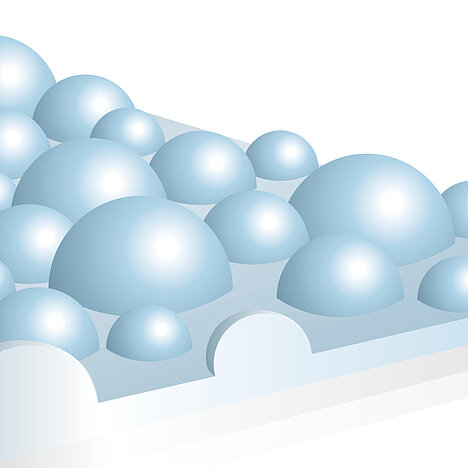
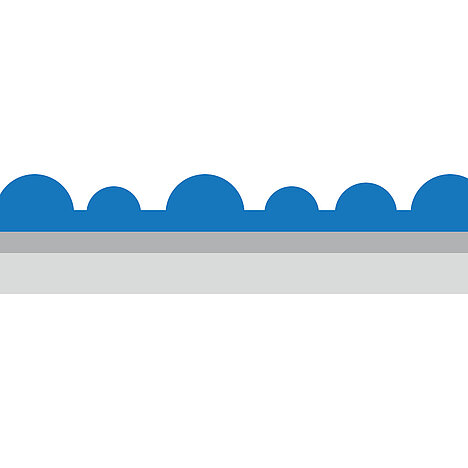
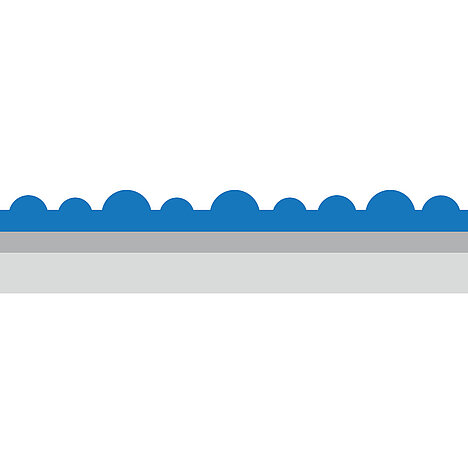

„soft“ topography for a fibre friendly surface
The expression „soft topography“ is to be understood in a figurative sense. Of course, this is a hard TOPOCROM® surface, too. But the structure of this Topocrom® coating is so gentle to fibres, filaments, non-wovens or films that we talk about a „soft“ surface. This coating is ideal for processing technical fibres such as carbon, basalt, glass or aramid.
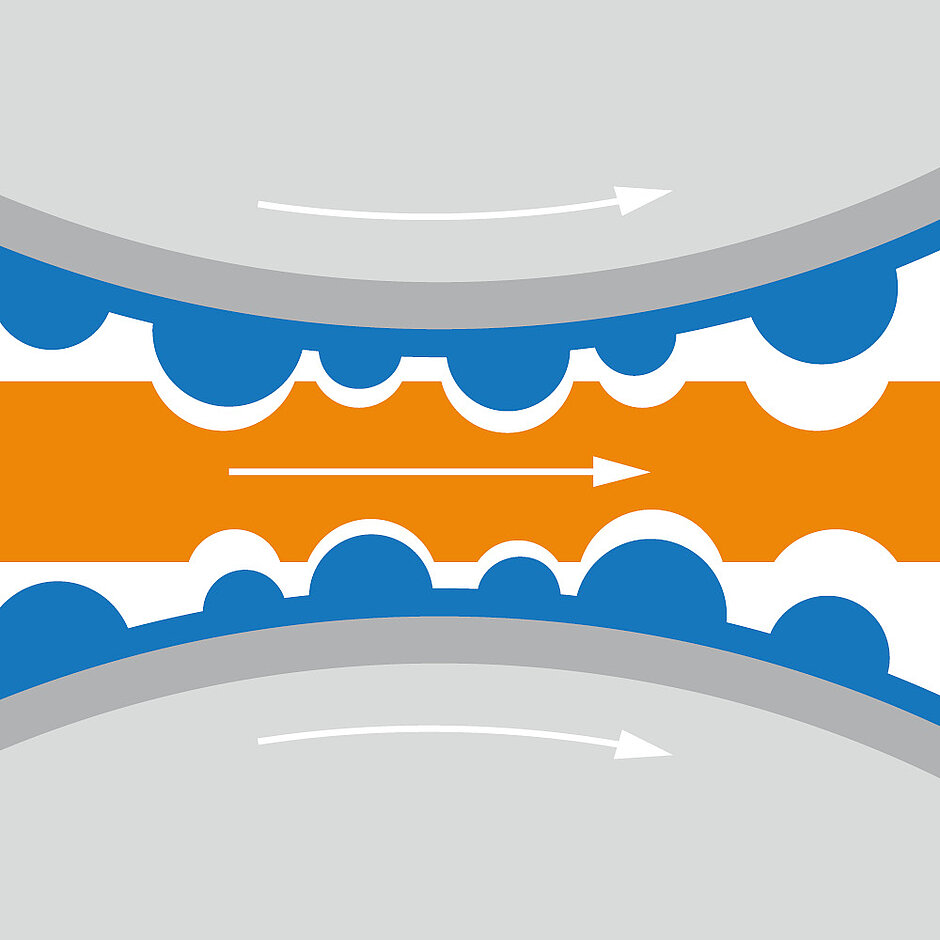
Embossing properties for the rolling process
In the steel industry TOPOCROM®-coated skin-pass rolls are used for the rolling process of thin sheet. In this way the structured surface is transferred into the sheet. These metal sheet surfaces considerably ameliorate the forming behaviour and form an ideal basis for modern painting (without filler, no moiré effect).
A suitable controlling system is necessary for the production of the individual surface properties and for the recall of data in case of repeat orders. For each demand the ideal surface topography is developed and saved in the computer.
Production method, coating times, galvanic processes, pre-treatment and finishing are reproducible with the identical result anytime. Thus the same surface is generated again and again.
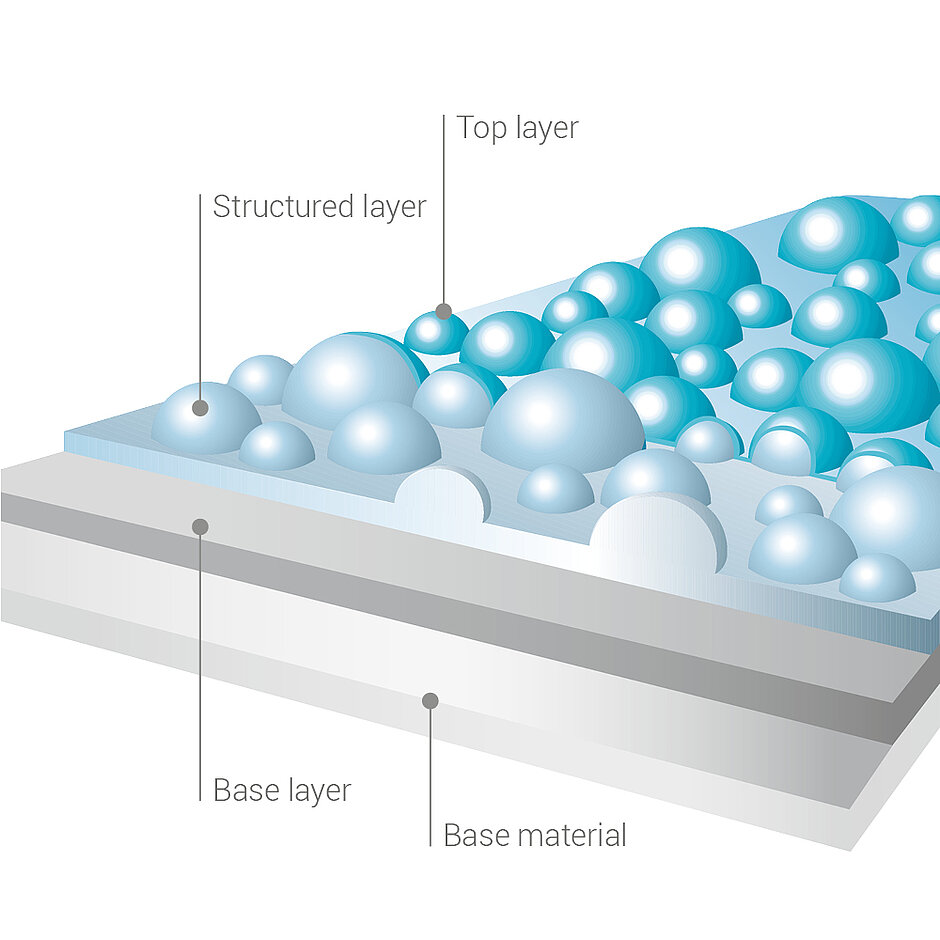
Layer construction in one working step
The construction of a layer system (base layer, structured layer, top layer) takes place in a single operation.
High suitability for rotation-symmetric work pieces
The process in the rotary reactor is ideal for coating rollers, rolls, thread guides or other rotation-symmetric respectively cylindrical elements. Also for the interior coating of pipes, this process technology is very suitable and approved.
This results in a variety of applications TOPOCROM®-process.
Energy-efficient surface coating without emissions
The TOPOCROM® process offers significant advantages in terms of environmental protection. The closed reactor process prevents contamination of people and the environment. The rinsing water is treated internally - through this and thanks to the closed electrolyte circuits, water consumption and waste quantities are reduced to the absolute minimum. During operation, only clean air is released into the environment after appropriate cleaning processes.
The surface coating in a single operation does not require any finishing. Thus, the material is used optimally. Last but not least, the process in a closed reactor is a particularly energy-efficient process compared to traditional electroplating.
Economical and durable surface coatings
The products coated according to the TOPOCROM® technology also contribute to the protection of the environment in everyday industrial life. Due to the specifically controlled properties and characteristics of the coating that are completely adjusted to the applications and the particular processes, machines with TOPOCROM® coated parts work very efficiently. This helps to save energy.
The particularly resistant surfaces also ensure long operating and service lives of the tools. As a result, fewer spare parts are needed.
Technical report with detailed information:
Process and systems engineering of TOPOCROM®
Corporate video with animated schematic representation of the TOPOCROM® process:
Work pieces, process and systems engineering